Benefits of Plastic Injection Moulding for Electronic Products
Using plastic injection molding to build parts for electrical systems has many benefits in terms of physical qualities, manufacturing process, environmental impact, and ability to market items
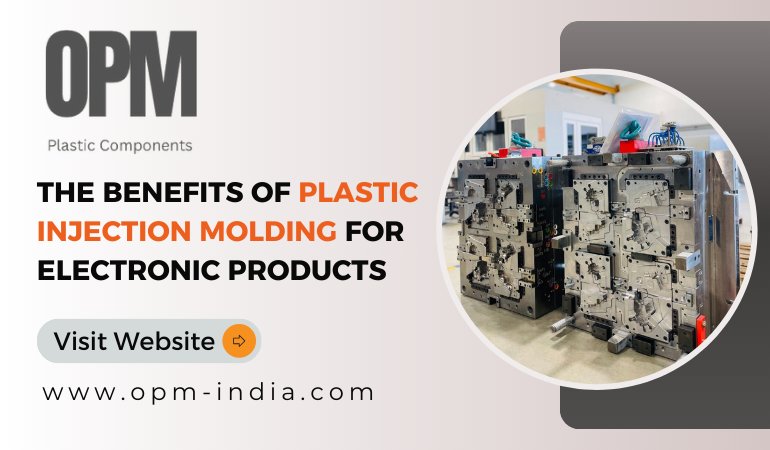
Plastic injection molding for electronics is an extremely effective and flexible manufacturing process that has transformed the electronics industry. With the growing demand for high-quality, high-volume electronic parts, injection molding services have become essential for producing a diverse range of products, from simple components to sophisticated assemblies. In this article, we will look at the advantages of plastic injection molding in the electronics sector, analyze different molding techniques, and dig into the realm of molded components.
Why use plastic injection molding for electronic products?
Using plastic injection molding to build parts for electrical systems has many benefits in terms of physical qualities, manufacturing process, environmental impact, and ability to market items. Here are the most important benefits of plastic injection molding for electronic products.
Reduces the final cost
The final plastic product is lighter than any other material that could have been used to produce it, such as steel. As a result, the method is the most cost-effective approach to produce a variety of forms in large quantities. Of course, certain materials are necessary for particular goods utilized in specialized industries such as aerospace. Nonetheless, for the vast majority of products, the unit cost of producing plastic products is the best and cheapest option.
Makes products energy-efficient
Plastic injection molding requires less energy than other materials like metal or wood.
Provides heat insulation
Overheating electrical appliances pose a risk in industries, offices, and households. Plastic, on the other hand, is a poor heat conductor, thus employing it at specific spots in electrical equipment is useful. In addition, the producer can employ a specific flame-retardant plastic during the plastic molding process to make electrical equipment safer and lower the risk of fire.
Provides electrical insulation
Plastic is a poor conductor of heat and electricity, therefore it acts as a sound barrier between a potentially lethal electrical current and the user. Again, selecting the appropriate resin is critical for electrical insulation, as specific resins are suggested for items including electrical wiring.
Creates durable products
Metals rust and biological things degrade, yet plastic is durable. Choosing a strong resin will make electronic products live longer. You can also choose chemically resistant polymers, which allow the products to be used in harsh situations.
Creates lightweight products
Original electronics manufacturers (OEMs) are constantly seeking to develop lighter goods. Making them out of plastic is one method to make them lighter without compromising durability. Different types of plastics can be utilized both inside and outside to create a lightweight product.
Creates hygienic products
Although not a major problem for most electrical items, plastic is a sanitary material since it is simple to remove bacteria and dirt from the surface. This is a critical aspect of electronic healthcare products, such as diabetic insulin pens.
Manufactures products quickly
Plastic injection molding enables you to make large quantities of a product quickly — the cycle time ranges from two seconds to five minutes, depending on the product’s complexity. Compared to cast iron, which has cycle lengths of more than 15 minutes, plastic goods are created quickly, allowing for the production of more products in less time.
Positive environmental outcomes
Plastic carries a poor reputation. While it is true that plastics have not been managed efficiently on a global scale, plastic injection molding can have favorable environmental effects when compared to other methods.
In addition, using recycled plastic in the plastic injection molding process is rather straightforward. Because there is always some color variation when utilizing recycled plastic, it cannot be utilized for essential external elements; however, it is an excellent choice for many internal components.
Plastic runners that would otherwise be discarded can be reground and combined with new plastic. The procedure lowers the cost of purchasing new plastic, saves time, and is energy efficient. However, OEMs and their EMS (electronics manufacturing services) partners should always negotiate this option before beginning a project, as the exact ratio of runner to virgin plastic that can be utilized is determined by the final product.
Aesthetically pleasing
Although the plastic used inside and outside electronic items is extremely useful, the sort of plastic used on the outside contributes to the product’s sales. It’s not simply utilized to hide the technology; it also makes the product appealing, causing people to want to buy it.
While beauty is subjective, plastic injection molding can help create aesthetically pleasing shapes and designs. A computer mouse, for example, can be made of various textures of plastic and have a high-gloss finish on one side. This is more likely to appeal to the customer.
Plastic injection molding simplifies the design and manufacture of plastic goods. The technique enables designers to be imaginative and creative while introducing new products to the market. If you want to make your product stand out by changing its shape, color, and texture or making it transparent, plastic injection molding is a great alternative. You can also put a variety of additives into the plastic to give the finished product a special quality.
Manufacturing Process: From Design to Production
The process of producing injection-molded electrical assemblies begins with the development of a comprehensive mold design. This design is then utilized to create a physical mold tool, which is meticulously manufactured and assembled to ensure perfect alignment and consistent outcomes throughout the injection molding process.
Once the mold tool is complete, plastic materials are heated and injected under high pressure into the cavity of the mold, hardening and taking on the appropriate shape. The molded components are then chilled, removed from the mold, and quality-checked before being assembled into the finished electronic product.
OPM — Your Partner in Electronics plastic injection molding manufacturing in India
As the demand for high-quality, high-volume electronic parts grows, plastic injection molding has emerged as an important production process in the electronics sector. Plastic injection molding for electronics is positioned to play an increasingly crucial role in the future of electronic device manufacture, thanks to its unequaled design flexibility, increased durability, and lower production costs. With OPM knowledge and commitment, you can be confident that your electronic components will be manufactured with a superior degree of quality and precision.
At OPM, we understand the need to provide reliable electrical components that fulfill today’s tight customer requirements. Our professional engineers and technicians are committed to delivering full injection molding services, including mold design, custom tooling, prototyping, and custom plastic injection molding.
These innovative components combine the durability of plastic with advanced electronics, creating products that are lightweight, functional, and versatile. For businesses aiming to leverage this technology, partnering with an expert electronics injection molding company in India is crucial.
Plastic injection molding is one of the most popular manufacturing methods used in many industries. This method allows plastic materials to be melted and injected into a mold to take the desired shape. Preferred in many sectors, from automotive to medical devices and electronics to toys, this method offers fast, efficient, and cost-effective production.
We also provide a variety of other services, such as mold decorating and the use of conductive inks, to help your electronic products stand out from the competition. Please contact us right away to learn more about Electronics Plastic Injection Molding and how we can help you improve your electronics production processes.
Conclusion:
The appliance industry requires many high-quality components to create the best electronics in the market. Electronics production is complex and needs advanced designs for aesthetic and functional purposes, and thermoplastic technology is the most popular choice. The durability of these materials in high temperatures, as well as their aversion to corrosion, allows them to stand out amongst other materials.
Plastic injection molding is an important aspect of the electronic industry, but producing high-quality goods fast requires the proper partner. At OPM, we create lasting relationships with our clients by providing white-glove service and delivering the quality parts electronics manufacturers need to compete in their industry.
Plastic injection molding manufacturers in India provide various benefits to electrical products, including high precision, cost-effectiveness, and scalability. Its ability to produce advanced and long-lasting components with minimal waste makes it a great option for firms seeking to optimize production while protecting quality.
Furthermore, the flexibility in material selection and the capacity to include innovative design features add to its popularity in the electronics industry. As technology develops, plastic injection molding remains a dependable and effective alternative for fulfilling the increasing needs of electronic product manufacturing.
Contact OPM Plastic Components today to discuss your requirements and discover how our expertise as an electronics plastic injection molding manufacturer in India can benefit your business. Contact us by email at sales@opm-uk.com or call us at +91–9900299893
What's Your Reaction?
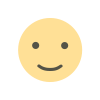
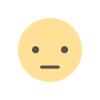
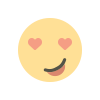
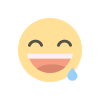
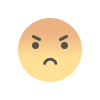
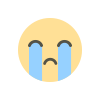
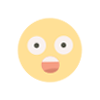